塑料注塑冷却器
In injection molding, our chiller is the key. It precisely controls mold temp within ±1°C, eradicating defects. Speeds up cooling, boosting production by 30%. Its energy-efficient design cuts consumption by 40%. Reduces thermal stress, prolonging equipment life. Elevate your molding, outperform rivals with our chiller.
You need an APT water chiller for your plastic injection moulding machine.

APT Water Chiller for the molding mould of plastic processing/injection machinery can:
- Greatly improve the surface finish of plastic products
- Reduce the surface striation and internal stress of plastic products
- Make the products Not Shrink or Deform
- Facilitate the demoulding of plastic products
- Accelerate the shaping of products, and greatly improve the production efficiency of plastic molding machine
How To Select The Appropriate Size Of Chiller According To The Mold Size Of Injection Molding Machine
1.Determine the Cooling Requirements of the Injection Molding Machine
Calculate the Heat Load:
During the operation of an injection molding machine, a large amount of heat is released when the plastic changes from a molten state to a cooled and solidified state. The formula for calculating the heat load (kW) is usually: , where is the mass of the plastic injected each time (kg), is the specific heat capacity of the plastic (kJ/(kg·°C)), and is the temperature difference between the melting temperature and the demolding temperature of the plastic (°C). For example, for common polypropylene (PP) plastic, the specific heat capacity is approximately . If 1 kg of PP plastic is injected each time, with a melting temperature of 200 °C and a demolding temperature of 40 °C, then the heat load . Since 1 kW = 1 kJ/s, assuming the cooling time is 10 s, the required cooling capacity is approximately.
Consider the Size and Complexity of the Mold:
Larger molds or those with complex internal structures require more cooling medium to ensure uniform cooling. Generally speaking, the larger the mold, the greater the cooling capacity required. For example, a small injection molding mold (with dimensions smaller than 300 mm×300 mm×300 mm) may require a cooling capacity of 3 – 5 kW, while a large injection molding mold for automotive parts (with dimensions larger than 1000 mm×1000 mm×1000 mm) may require a cooling capacity of 30 – 50 kW.
2.Pay Attention to the Specification Parameters of the Injection Molding Machine
Clamping Force:
The clamping force is a key parameter of the injection molding machine, which is related to the size of the injection molding machine and the size of the products it can produce. Usually, the larger the clamping force, the larger the specification of the injection molding machine, and the greater the cooling capacity required for the chiller. For example, an injection molding machine with a clamping force between 100 and 300 tons may be paired with a chiller with a cooling capacity of 8 – 15 kW; while a large injection molding machine with a clamping force exceeding 1000 tons may require a cooling capacity of 30 – 50 kW.
Injection Volume:
The injection volume reflects the amount of plastic injected by the injection molding machine each time. The larger the injection volume, the higher the energy required for cooling. Generally, it can be estimated according to the amount of cooling capacity required for each kilogram of plastic. For example, approximately 10 – 15 kW of cooling capacity is needed to cool each kilogram of plastic (this is only a rough estimate, and it will actually vary depending on factors such as the type of plastic).
3.Consider Production Efficiency and Cycle Time
Production Speed:
If the injection molding machine has a high production speed and a short cycle time, then the number of cooling requirements per unit time will be high, and the requirements for the cooling capacity and response speed of the chiller will be high. For example, a high-speed injection molding machine that can complete 3 – 5 injection cycles per minute requires the chiller to be able to quickly remove heat to ensure the cooling effect of each cycle.
Proportion of Cooling Time in the Cycle:
It is important to understand the proportion of cooling time in the entire cycle during the injection molding process. If the cooling time accounts for a large proportion, a more powerful cooling capacity is needed to shorten the cooling time and improve production efficiency. For example, when the cooling time accounts for more than 50% of the cycle, it is necessary to ensure that the cooling capacity of the chiller can fully meet the need for rapid cooling during this period.
4.Requirements for Temperature Control Precision
Product Quality Requirements:
For some injection molded products with high requirements for dimensional accuracy and appearance quality, such as the casings of electronic products and precision optical parts, precise mold temperature control is required. In this case, a chiller with high temperature control precision should be selected, and generally, the temperature should be controlled within ±1 – ±2 °C. For some products with relatively low requirements for dimensional and appearance accuracy, such as ordinary plastic toys, a temperature control precision within ±3 – ±5 °C may be sufficient.
Clamping Force | Injection Volume (g) | Capacity of Water - Cooled Chiler (HP) | Capacity of Air - Cooled Chiler (HP) |
---|---|---|---|
NT80B | 119~140 | 5 | 5 |
NT120B | 202~231 | 5 | 5 |
NT150 | 233~330 | 5 | 5 |
NT200 | 340~508 | 5 | 8 |
NT250 | 541~755 | 8 | 8 |
NT330 | 687~935 | 10 | 15 |
NT380 | 1026~1367 | 10 | 15 |
NT450 | 1419~1946 | 15 | 20 |
NT560 | 2174~2437 | 15 | 20 |
NT720 | 3074~3795 | 25 | 30 |
NT1000 | 4333~5199 | 30 | 40 |
Ordinary, injection molding machine clamping force between 80 tons and 100 tons of machines equipped with the machine is 5HP
<<There is a table for your reference
You should know the kinds of raw materials used and the quantity used per hour. That would be more accurate, won’t waste energy efficiency.
Water Cooling Box Type Industrial Water Chiller For Injection Molding Machine

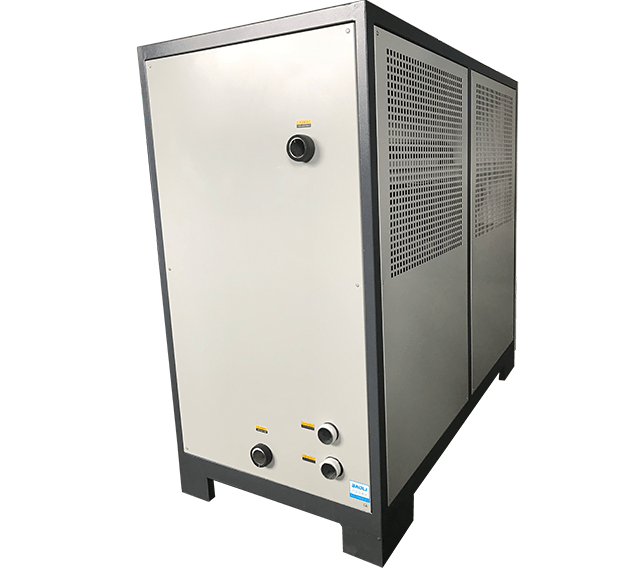
Compact Structure, Long Service Life, High Energy Saving Efficiency
- Original compressor: environmental protection, high stability, long life, power saving and energy saving [Daikin, Copeland, national, maneurop, Sanyo];
- Low energy consumption water pump: large flow and high head, to meet the water conditions of various equipment;
- High precision pressure controller: protect compressor and main components accurately and quickly;
- Microcomputer temperature controller: it can control water temperature from + 3 ° C to + 25 ° C with display accuracy of 0.1 ° C;
- Shell and tube condenser: spiral copper tube has strong heat transfer efficiency, long service life, easy cleaning and maintenance, and is the main component of traditional central air conditioning;
- Stainless steel water tank coil evaporator: easy to clean and maintain, clear understanding of the actual situation of water equipment;
- Protection device: voltage undervoltage, power supply phase loss, wrong phase protection, compressor current overload protection, pump current overload protection, high and low pressure protection, antifreeze protection, insufficient cooling water flow, insufficient chilled water flow protection, and delayed start-up, etc. safety protection device can alarm and display fault.
Technical Parameter for 3-100HP Water-Cooled Chiller
模型 | aptbl-1FC | aptbl-2fcs | aptbl-3FC | aptbl-5FC | aptbl-8fcd | aptbl-10fcd | aptbl-12fcd |
---|---|---|---|---|---|---|---|
Cooling Capacity | 2500 W | 5000 W | 7500 W | 12500 W | 20000 W | 25000 W | 30000 W |
压缩机电机 | 0.8 KW | 1.6 KW | 2.4 KW | 4 KW | 6.4 KW | 9 KW | 9.6 KW |
冷水流 | 7.2 L/min | 14.4 L/min | 21.6 L/min | 36 L/min | 58 L/min | 72 L/min | 86 L/min |
冷冻水中/外管 | 1" inch | 1" inch | 1" inch | 1" inch | 1" inch | 1.5" inch | 1.5" inch |
泵电动机 | 0.5 HP | 0.5 HP | 0.5 HP | 0.5 HP | 1 HP | 1 HP | 1 HP |
水箱容量 | 20 L/min | 40 L/min | 45 L/min | 50 L/min | 100 L/min | 120 L/min | 150 L/min |
净重 | 73 Kg | 106 Kg | 165 Kg | 195 Kg | 410 Kg | 450 Kg | 550 Kg |
Dimension "L*W*H (mm)" | 850*520*900 mm | 850*520*900 mm | 900*520*800 mm | 1200*680*1100 mm | 1300*700*1300 mm | 1300*700*1300 mm | 1600*750*1500 mm |
电源 | 220V/50Hz | 220V/50Hz | 220V/50Hz | 3N-380V/50Hz | 3N-380V/50Hz | 3N-380V/50Hz | 3N-380V/50Hz |
制冷剂 | R22/R407C/R410A/R134A | ||||||
节气门设备 | 毛细管/膨胀阀 | ||||||
冷凝器 | 鳍管型气冷冷凝器 | ||||||
蒸发器 | Stainless steel water tank copper coil evaporator |
模型 | aptbl-15fcd | aptbl-20fcd | aptbl-25fcd | aptbl-30fcd | aptbl-40FCD | aptbl-45FCD | aptbl-50fcd |
---|---|---|---|---|---|---|---|
Cooling Capacity | 37500 W | 50000 W | 62500 W | 75000 W | 100000 W | 112500 W | 125000 W |
压缩机电机 | 12 KW | 16 KW | 20 KW | 24 KW | 32 KW | 36 KW | 40 KW |
冷水流 | 108 L/min | 143 L/min | 180 L/min | 216 L/min | 288 L/min | 323 L/min | 360 L/min |
冷冻水中/外管 | 2" inch | 2.5" inch | 2.5" inch | 3" inch | 3" inch | 4" inch | 4" inch |
泵电动机 | 2 HP | 3 HP | 3 HP | 5 HP | 5 HP | 7.5 HP | 7.5 HP |
水箱容量 | 200 L/min | 300 L/min | 350 L/min | 400 L/min | 500 L/min | 600 L/min | 800 L/min |
净重 | 670 Kg | 780 Kg | 860 Kg | 960 Kg | 1050 Kg | 1100 Kg | 1200 Kg |
方面 | 1900*900*1600 mm | 2100*1000*1700 mm | 2100*1000*1700 mm | 2500*1000*1700 mm | 2600*1000*1800 mm | 2800*1000*1800 mm | 2800*1000*1800 mm |
电源 | 3N-380V/50Hz | ||||||
制冷剂 | R22/R407C/R410A/R134A | ||||||
节气门设备 | 毛细管/膨胀阀 | ||||||
冷凝器 | 鳍管型气冷冷凝器 | ||||||
蒸发器 | Stainless steel water tank copper coil evaporator |
1. The cooling capacity is based on the following standard temperature conditions :
1)Chilled water return temperature 12 ° C, Chilled water outlet temperature 7 ° C
2)Cooling water inlet temperature 30 ° C , Cooling water inlet temperature 35 ° C
2. Scope of working Temperature
1)Cooling water outlet temperature 22 ° C to 37 ° C , Cooling water temperature difference 3.5 ° C to 6.5 ° C
2)Chilled water outlet temperature 5 ° C to 20 ° C , Chilled water outlet temperature difference 2.5 ° C to 7 ° C