Thermal Spray Chillers: Precision Cooling Solutions
Water chillers for thermal spray coatings are essential for maintaining precise temperature control during the coating process. At APTWaterChiller, our advanced thermal spray cooling systems ensure optimal performance, enhancing efficiency and coating quality for industrial applications. Whether you’re working with plasma, HVOF, or arc spraying,
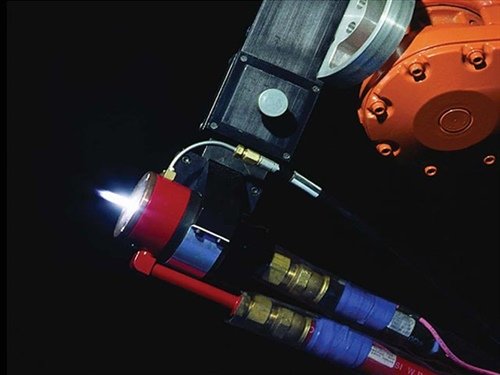
How to Select the Optimal Chiller System for Thermal Spray Systems?
--A Design Guide for Metco F4, Praxair SG-100、7700 and JP-8000
Why would Thermal spray Process required cooling systems?
Thermal spray coating is a critical process used across industries like aerospace, automotive, energy, and manufacturing to apply protective coatings that enhance durability, corrosion resistance, and thermal insulation. However, maintaining precise temperature control during thermal spray processes—such as HVOF (High-Velocity Oxygen Fuel), plasma spray, and arc spray—is essential to prevent equipment overheating, nozzle clogging, or coating defects. This is where our APTBL series water chillers come into play, offering reliable, efficient, and customizable cooling solutions tailored to your thermal spray needs.
- Nozzle Temperature Control: Overheating can melt spray nozzles, while over-cooling can lead to clogging or inconsistent coating quality.
- Equipment Longevity: High operating temperatures accelerate wear on spray guns and related hardware.
- Process Consistency: Variations in temperature affect coating adhesion, density, and uniformity.
- Water Quality Issues: Using untreated city water can introduce corrosives or particulates, damaging cooling systems and reducing accuracy.
Traditional cooling methods, such as single-pass city water systems, often fall short due to maintenance costs and inefficiency. Our APTBL series chillers address these pain points with innovative design and performance.

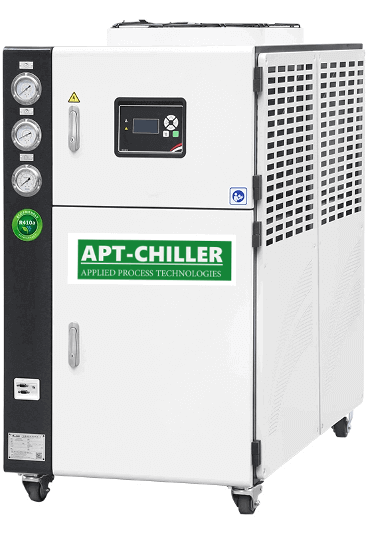
How can a water chiller help thermal spraying?
- Precise Temperature Regulation: Equipped with programmable controllers and closed-loop sensor feedback, our chillers maintain consistent nozzle temperatures, ensuring optimal coating performance.
- Customizable Design: From high-pressure, low-volume pumps to non-ferrous piping and deionized water compatibility, we tailor solutions to your specific thermal spray setup.
- Energy Efficiency: Variable speed drives and efficient heat exchangers reduce energy consumption, lowering operational costs.
- Durability: Built with stainless steel components and corrosion-resistant materials, our chillers withstand the rigors of continuous operation, extending equipment lifespan.
- Versatility: Suitable for HVOF, plasma spray, and arc spray applications
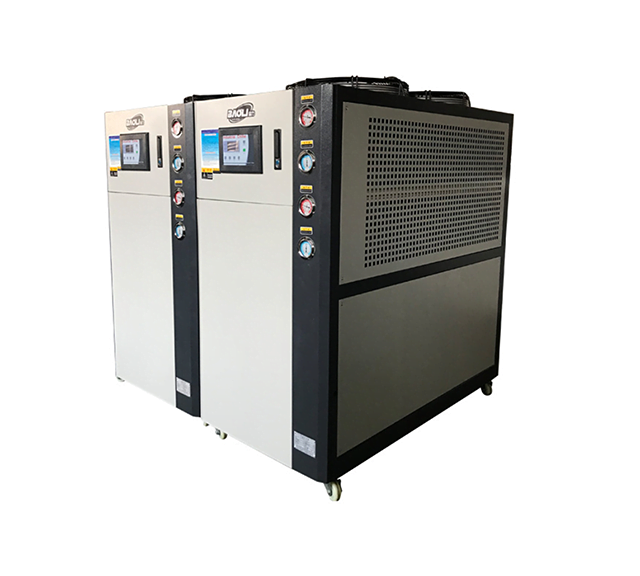
Water Chiller Selection for Different Thermal Spray Processes
1. High-Velocity Oxygen Fuel (HVOF) Spray
- Process Characteristics: HVOF uses a high-pressure combustion jet (up to 3000°C) to propel particles at supersonic speeds, creating dense, high-adhesion coatings (e.g., for aerospace turbine blades).
- Cooling Requirements:
High Heat Load: The intense combustion generates significant heat, requiring robust cooling for the spray gun and nozzle.
Precise Temperature Control: Maintaining 15-25°C water temperature prevents thermal distortion and ensures coating uniformity.
High Flow Rate: Needs 500-2000 L/h depending on gun size and powder feed rate.
2. Plasma Spray
- Process Characteristics: Plasma spray uses an electric arc to ionize gas, creating a plasma jet (up to 15000°C), ideal for ceramic and metallic coatings (e.g., thermal barriers).
- Cooling Requirements:
Moderate to High Heat Load: The plasma torch generates substantial heat, necessitating efficient cooling of the anode, cathode, and powder injector.
Temperature Stability: Target 10-20°C to prevent electrode erosion and maintain coating integrity.
Moderate Flow Rate: Typically 300-1500 L/h, depending on torch power (20-80 kW).
3. Flame Spray
- Process Characteristics:Flame spray uses a fuel-oxygen flame (around 3000°C) to melt wire or powder, suitable for general-purpose coatings (e.g., anti-corrosion layers).
- Cooling Requirements:
Lower Heat Load: Compared to HVOF or plasma, flame spray generates moderate heat, requiring less aggressive cooling.
Flexible Temperature: 20-30°C is sufficient, with less stringent stability needs.
Low to Moderate Flow Rate: 200-1000 L/h, depending on wire feed speed.
4. Arc Spray
- Process Characteristics: Arc spray uses an electric arc between two wires to melt material, creating coatings for corrosion and wear resistance (e.g., bridge cables).
- Cooling Requirements:
Moderate Heat Load: Heat is localized at the arc point, requiring cooling for the gun and cables.
Temperature Range: 15-25°C to prevent wire oxidation and ensure consistent melting.
Moderate Flow Rate: 400-1200 L/h, depending on wire diameter and spray rate.
